Copper wire production is one of the fundamental processes in the electrical and electronics industries, playing a pivotal role in electrical current transmission and various industrial applications. This intricate process involves several precise stages, starting from the extraction of raw copper to the production of high-quality copper wires. Not only does this process support the electrical sector, but it is also widely utilized in the manufacturing of electronic components, connectors, and even automotive industries. In this article, we will explore the various stages of copper wire production along with the related equipment to shed light on its importance and detailed processes.
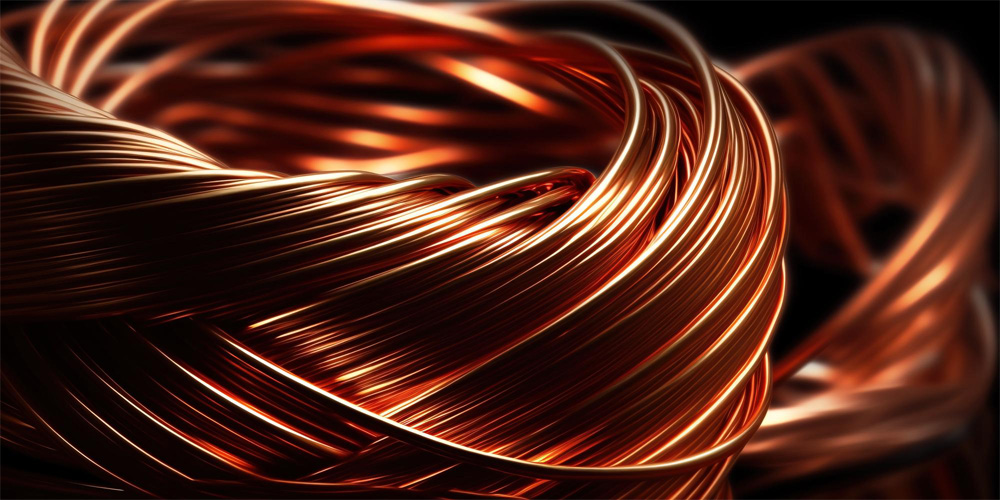
Copper Wire Manufacturing Process
Step 0: Extraction of Raw Copper
The first step in copper wire production is the extraction of raw copper from mines. The mined copper ore typically contains impurities that must be removed during subsequent processing stages. The ore is crushed and ground into finer particles to facilitate processing. This foundational step often involves advanced mining technologies to separate pure copper from other compounds. The quality of the extracted copper at this stage significantly impacts the final quality of the copper wire.
Step 1: Smelting and Refining
In this stage, crushed copper ore is melted in specialized furnaces. The process separates pure copper from impurities. Techniques such as electrolytic refining are employed to produce high-quality copper rods. In this method, pure copper cathodes meeting high standards are produced. ETP copper rod is commonly manufactured at this stage, utilizing modern technologies to ensure the final copper is of high purity and optimal conductivity.
Step 2: Converting Copper Sulfate to Copper Cathodes
A critical stage in copper wire production is converting copper sulfate into copper cathodes. This process yields highly pure copper that can be drawn into wires and rods. These cathodes are further processed into rods of the desired dimensions and quality. This step also incorporates stringent quality control measures to ensure the copper cathodes meet industrial standards.
Step 3: Drawing Process
In this stage, copper cathodes are transformed into copper wires. These rods are drawn through a process that reduces their diameter to various sizes. The drawing process involves not only physically stretching the wires but also using lubricants and temperature control to minimize friction and prevent damage to the wires. The quality of these wires has a direct impact on the performance of the final copper wire product.
Step 4: Annealing and Controlled Cooling
To enhance flexibility and reduce internal stresses, copper wires undergo an annealing process. This involves controlled heating and cooling, resulting in annealed copper rod, which is highly suitable for sensitive industrial applications. Annealing, as a crucial phase of copper wire production, improves electrical conductivity and resistance to fatigue, ensuring the wires meet high-performance standards.
Step 5: Categorization and Bunching
After drawing and annealing, copper wires are categorized and twisted into strands. This process enhances mechanical strength and improves the electrical properties of the wires. This stage often includes twisting the wires into different shapes depending on their final application. Moreover, precise quality checks are conducted during this stage to ensure the wires meet the required standards.
Step 6: Tin Coating
To improve resistance to corrosion and enhance conductivity, copper wires are coated with tin. This stage involves processes such as hot-dip tinning or electroplating, which provide the wires with a protective tin layer. This ensures the wires are more resistant to rust and oxidation, significantly extending their lifespan. Any copper waste generated during this stage is meticulously recycled.
Step 7: Twisting and Braiding
In this stage, copper wires are twisted or braided into various forms. This method increases flexibility and functionality in industrial settings. The process involves advanced machinery and modern techniques to produce high-quality braided wires. Braided wires are typically used in applications requiring high flexibility and mechanical strength.
Step 8: Insulation and Coating
Finally, copper wires are insulated and coated for use in various industries. This last stage ensures the wires are resistant to different environmental conditions while providing optimal performance. Depending on the requirements, coatings can be made from materials such as PVC, rubber, or specialized polymers.
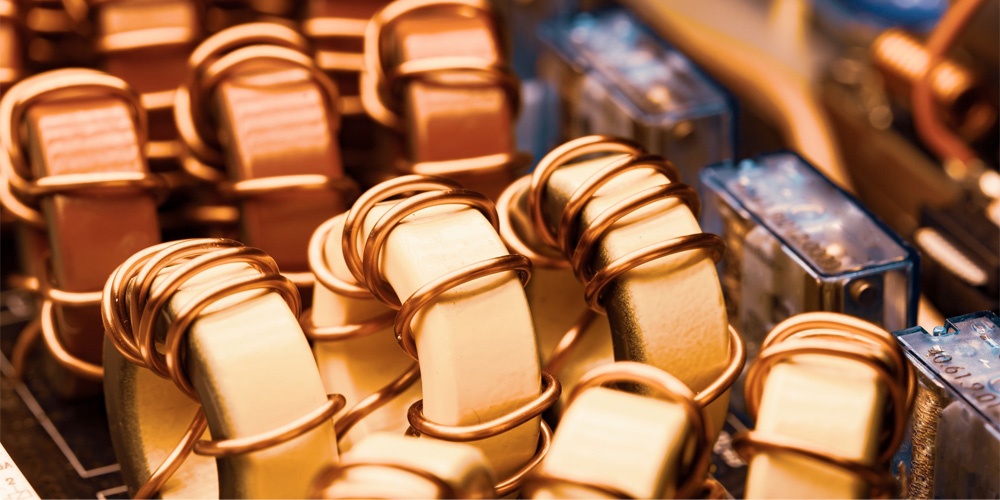
Equipment for Copper Wire Production
Like any manufacturing process, copper wire production requires specialized equipment to ensure efficiency and quality. Below is a list of essential equipment used in the production process:
- Primary wire drawing machine
- Medium wire drawing machine
- Continuous fine wire annealing machine
- Final fine wire drawing machine
- Multi-wire drawing machine
- Buncher wire machine
- Hot weld and wire thinning machine for wire joining
- Cold welding machine for wire joining
- Quality control and testing equipment
- Shrinking machines
Conclusion
The production of copper wire is a multi-stage and precise process that begins with raw copper extraction and continues through insulation and final coating. This process requires advanced equipment and meticulous management to ensure high-quality products. Kayhanmetal, as a copper supplier, offers a variety of copper wires and rods, including copper rod 1.8 mm, copper rod 2.6 mm, and copper rod 8 mm. Additionally, if you are interested in purchasing copper scrap, you can contact us. Utilizing copper scrap in the production process can help reduce costs and conserve natural resources. Attention to detail at every stage ensures that the final product is of the highest quality and ready to serve a wide range of industries.
No comment