In the world of electrical and structural applications, the choice of material plays a pivotal role in determining the success and efficiency of any project. Among the most commonly debated materials are copper rods and aluminum rods, each offering distinct strengths and weaknesses. Copper is often celebrated for its superior electrical conductivity, durability, and resistance to corrosion, making it a favorite for high-performance electrical systems. On the other hand, aluminum stands out for its lightweight nature, affordability, and versatility, especially in large-scale projects where cost-effectiveness is crucial. Choosing between these two materials is not a one-size-fits-all decision; it depends on a range of factors such as conductivity, cost, weight, durability, and specific project requirements. For example, while copper may be the go-to choice for electrical wiring in residential buildings, aluminum might be preferred in applications like power transmission lines due to its lighter weight and lower cost.
In this article, we’ll delve deeper into the detailed comparison of copper rod vs aluminum rod, examining their physical and chemical properties, advantages and disadvantages, and their suitability for different applications. By understanding these aspects, you’ll be better equipped to choose the ideal material for your project and ensure its long-term success.
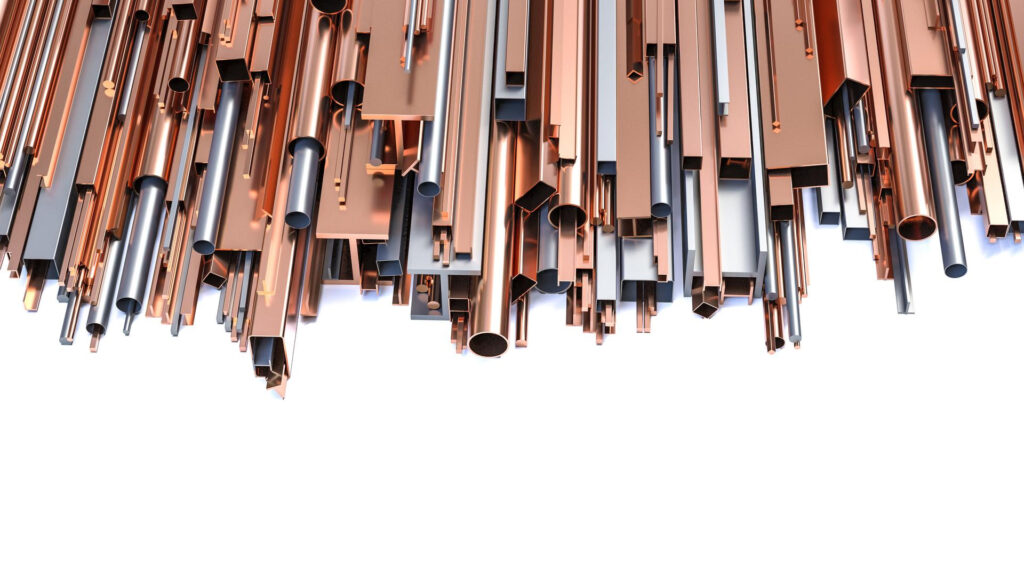
Copper Rod vs Aluminum Rod: Key Differences
The primary difference between copper rod and aluminum rod lies in their electrical conductivity and weight. Copper, celebrated for its exceptional conductivity, is the top choice for critical electrical applications, such as power transmission and electronics. Aluminum, however, is significantly lighter and more cost-effective, making it a practical solution for large-scale projects where weight and budget play a pivotal role.
Another distinguishing factor is tensile strength. Copper boasts a higher tensile strength, ensuring its suitability in demanding environments where durability is paramount. While aluminum may lack the same strength, it compensates with its inherent corrosion resistance, especially when treated with proper finishes. This quality makes aluminum ideal for outdoor or industrial uses where exposure to environmental elements is unavoidable.
Overall, choosing between copper and aluminum rods depends on specific project requirements, balancing conductivity, weight, durability, and cost considerations.
Conductivity: Copper vs Aluminum
When it comes to electrical conductivity, copper is widely recognized as the superior material. Copper’s high conductivity allows it to carry electrical current efficiently, making it an ideal choice for applications that require reliability and performance, such as copper service wire, copper SE cable, and copper wiring in a variety of electrical systems. Its ability to transmit electricity with minimal resistance ensures energy efficiency and reduces power loss, which is especially critical in residential, commercial, and industrial applications.
On the other hand, while aluminum has lower electrical conductivity than copper, it still holds an important place in the electrical industry. Aluminum’s main advantage lies in its light weight and cost-effectiveness. As a result, materials like aluminum underground wire and direct burial aluminum wire are often used in large-scale installations, particularly for long-distance transmission lines. These types of cables are advantageous for projects where cost savings and ease of installation are key considerations, as aluminum is much lighter and less expensive than copper.
Though aluminum’s conductivity is not as high as copper’s, it can still carry a significant electrical load in many situations. Additionally, aluminum is often used in applications where weight is a concern, such as in overhead transmission lines or areas with challenging installation conditions. To mitigate its lower conductivity, aluminum wiring is often made with a larger gauge than copper wiring, ensuring that it can still handle the required electrical load.
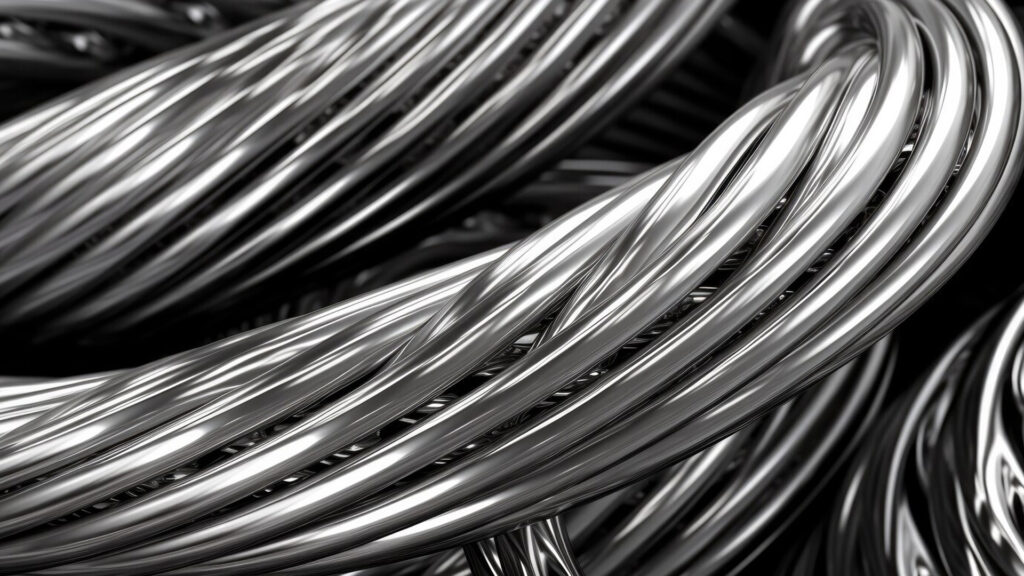
Cost and Budget Considerations
When choosing between copper rod vs aluminum rod, cost is one of the most critical factors to consider. Copper, due to its excellent conductivity and strength, tends to be more expensive than aluminum. This higher cost can be justified in situations where long-term reliability and performance are essential. For example, copper is often the preferred material for applications like 200 amp service entrance cables in high-amperage installations, where its durability and conductivity ensure consistent performance over time, even under demanding conditions.
However, aluminum rods offer a more budget-friendly alternative. While aluminum is not as conductive or strong as copper, it remains a viable option for many installations, especially when cost is a significant concern. For large-scale electrical projects, such as 200 amp aluminum service wire installations, aluminum can provide significant cost savings. While it may not offer the same level of performance as copper, aluminum still delivers acceptable conductivity and reliability for most residential and commercial applications. This makes aluminum a popular choice for budget-conscious projects where performance requirements are not as stringent.
Durability and Longevity
Copper is renowned for its durability and resistance to wear and tear. It’s a preferred material for applications like copper service entrance wire, where longevity is crucial. Aluminum, while less durable, can be treated to resist corrosion. In environments with moisture exposure, aluminum service wire and direct burial aluminum service wire can be treated with protective coatings to enhance their lifespan.
Applications in Electrical Systems
Both copper and aluminum rods play vital roles in electrical systems, each offering unique benefits depending on the application. The choice between these materials is often influenced by factors such as conductivity, cost, and specific performance requirements. Below are some key areas where these materials are commonly used:
· Service Entrance Cables: Service entrance cables are crucial for bringing electrical power into a building or facility. Copper is often the material of choice for these cables due to its superior electrical conductivity, which ensures optimal performance and reliability in power distribution. Copper cables also have greater durability and are resistant to corrosion, which makes them ideal for long-term installations. However, in larger projects, aluminum is frequently considered a more cost-effective alternative, as it is lighter and significantly cheaper than copper. This cost advantage makes aluminum a viable option in situations where the cable runs are longer, and the higher conductivity of copper is not as critical.
· Feeder Wires: Feeder wires are used to carry electricity from the service entrance to the various circuits within a building. Copper feeder wires are preferred in applications where high conductivity and consistent performance are paramount, especially in demanding environments where electrical systems are required to handle significant loads. Copper’s lower resistance helps minimize power loss, which is essential for maintaining efficiency. On the other hand, aluminum feeder wire is commonly chosen for its lower cost and lighter weight compared to copper, which can reduce overall project expenses. Aluminum is particularly advantageous in situations where long distances need to be covered, as its lower cost helps make large-scale installations more economical, while still meeting the necessary power demands.
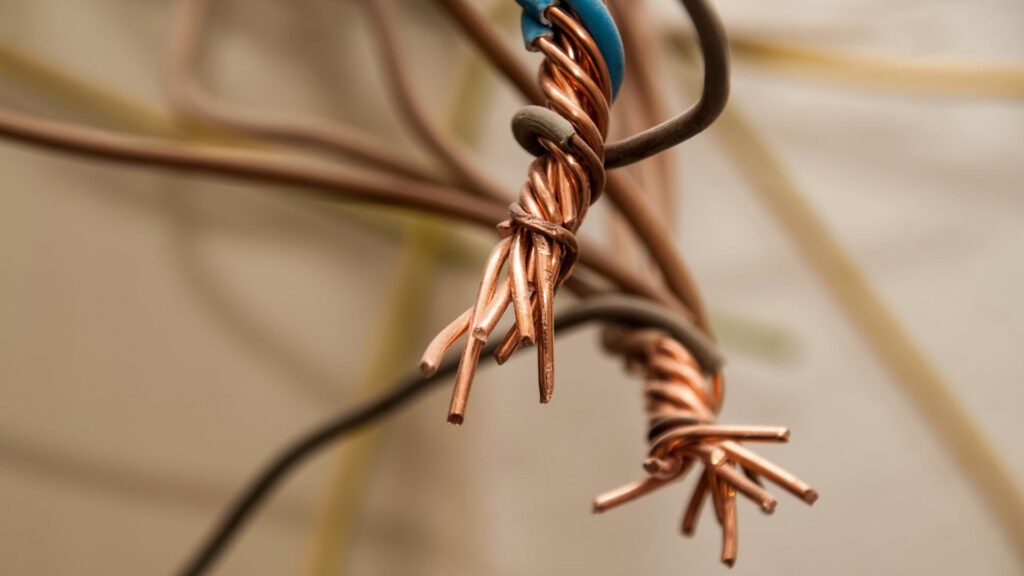
Copper Rod vs Aluminum Rod :Environmental Impact
In today’s environmentally conscious world, the sustainability of materials is a growing concern. Copper mining has a higher environmentalfootprint compared to aluminum production. Aluminum’s recyclability and lower production energy requirements make it a greener option for projects wheresustainability is a priority.
Choosing between copper rod vs aluminum rod boils down to your project’s specific needs. If conductivity, durability, and long-term performance are your priorities, copper is the ideal choice. However, if budget constraints and lightweight material are more critical, aluminum provides a practical and cost-effective solution.
For applications like aluminum service entrance wire, direct burial aluminum wire, or 200 amp service entrance cable copper, it’s crucial to evaluate the requirements and make an informed choice. By understanding the strengths and weaknesses of each material, you can ensure optimal performance and efficiency in your projects.
conclusion
In conclusion, when looking to purchase high-quality materials such as 8 mm copper rod, 1.8 mm copper rod, 2.6 mm copper rod, and Copper Scrap, Kayhanmetal is a trusted and reputable source. Known for offering top-notch products, they provide a reliable option for all your copper and scrap needs, ensuring you get the best quality at competitive prices.
Frequently Asked Questions
Which is better for service entrance wires: aluminum or copper?
Copper is preferred for its higher conductivity and durability,
but aluminum is a more cost-effective option for larger projects.
What is the difference in tensile strength between copper and aluminum?
Copper has a higher tensile strength, making it more suitable for
demanding environments, while aluminum is more resistant to corrosion but lacks
the same strength.
Can aluminum replace copper in electrical applications?
Yes, aluminum can be used in many electrical applications,
especially in large-scale projects where lower cost and lighter weight are
important.
No comment