Why Are Copper Standards Important?
Copper wires are among the most critical components in the electrical and electronic industries, playing a key role in the transmission of electricity and data. Given the sensitivity of their performance, ensuring their quality and safety is a necessity. In this context, copper standards are recognized as global benchmarks for evaluating the quality and performance of copper wires.
These standards not only ensure consumer safety but also optimize the efficiency and longevity of copper products. Without clear standards, copper manufacturers would face challenges such as reduced customer trust and increased risks of technical failures. In this blog, we explore the key international standards established to evaluate the quality and safety of copper wires. These standards help manufacturers produce higher-quality products and play a vital role in the growth of related industries.
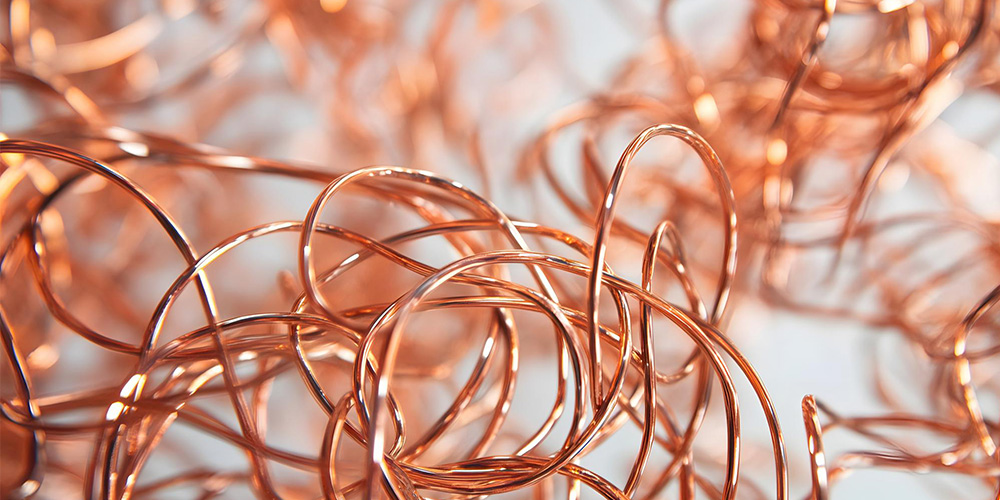
Key International Standards for Copper Wires
1. IEC Standards (International Electrotechnical Commission)
IEC standards, developed by the International Electrotechnical Commission, focus on material quality, electrical conductivity, corrosion resistance, and safety of copper wires. These standards are widely used in the electrical and electronic industries, ensuring that copper wires deliver stable and reliable performance.
2. ASTM Standards (American Society for Testing and Materials)
ASTM has established standards for evaluating the physical and chemical properties of copper and its products. Notable standards include:
- ASTM B1: For bare copper wire
- ASTM B2: For annealed copper wire
3. ISO Standards (International Organization for Standardization)
ISO provides global benchmarks for product quality and compatibility. Key standards related to copper wires include:
- ISO 431: Quality assessment of industrial copper materials
- ISO 9001: Quality assurance in manufacturing processes
4. BS Standards (British Standards)
British Standards focus on the quality, safety, and electrical conductivity of copper wires. They are widely applied in large engineering projects and copper product exports. An example is:
- BS EN 13602: Standard for annealed copper wires
5. DIN Standards (Deutsches Institut für Normung)
German DIN standards are critical for defining the specifications of copper wires. These standards provide detailed information on copper quality, electrical conductivity, and mechanical resistance.
The Application of Copper Standards to Copper Rods
International standards also apply to copper rods, ensuring the quality, mechanical strength, and safety of these products. While copper wire standards emphasize conductivity and electrical properties, copper rod standards account for factors like wall thickness, pressure resistance, and environmental adaptability. Copper rods in various sizes, such as 1.8 mm copper rod, 2.6 mm copper rod, and 8 mm copper rod, must be manufactured according to these standards to meet industrial requirements.
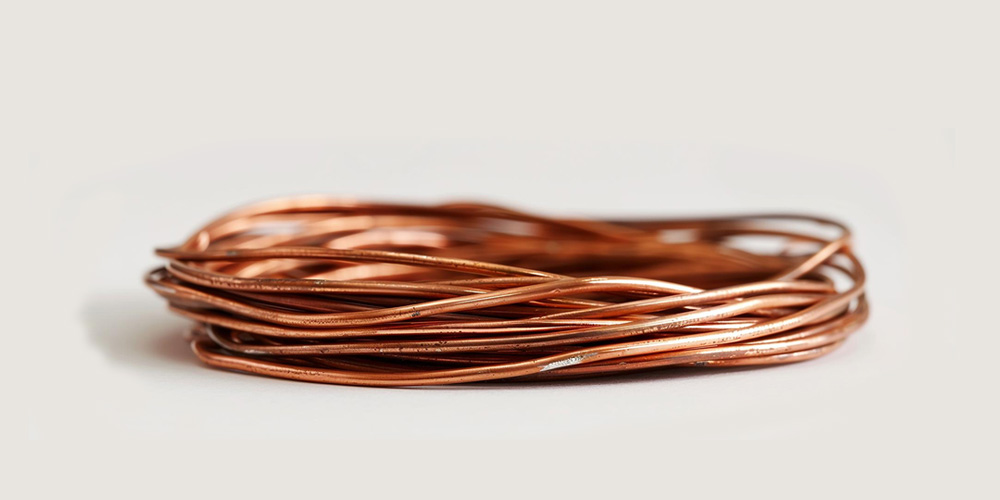
Factors Influencing Compliance with Standards
To produce copper products that meet international standards, several critical factors come into play. The quality of raw materials is one of the most important; utilizing high-purity copper without impurities ensures the production of premium products. Additionally, the production process must be meticulously monitored and employ advanced technologies. Precise control of temperature, pressure, and other manufacturing parameters ensures that the final product meets specified standards. Furthermore, performing quality control tests at various stages of production is essential. These tests include evaluating electrical resistance, thickness, mechanical strength, and product durability, all of which confirm compliance with copper standards.
Benefits of Adhering to Copper Standards for Manufacturers
Adherence to international standards offers significant advantages to copper manufacturers. It boosts customer trust as standardized products guarantee quality and safety, making consumers more likely to choose them. Furthermore, compliance reduces costs associated with product defects or failures. By producing standard-compliant products, issues like product returns or customer complaints are minimized. Finally, having certifications for international standards enables manufacturers to compete in global markets. This increases market share and revenue, allowing manufacturers to establish themselves alongside leading global brands.
Conclusion
This article explored the importance of copper standards in producing copper wires and copper rods, highlighting their role in ensuring quality, safety, and performance. International standards play a pivotal role in improving raw material quality, enhancing production processes, and increasing competitiveness in global markets. Compliance with these standards not only reduces costs associated with defective products but also builds customer trust.
At Kayhanmetal, we utilize advanced methods like ETP Copper Rod and Annealed Copper Wire to produce high-quality copper wires and copper rods that meet global standards. Additionally, you can purchase copper scrap from us, ensuring top-tier quality for your industrial needs. Trust our products and services for a unique experience of quality and reliability!
No comment